
Supply Chain Management (SCM)
- Yasser Quol
- Mar 21, 2021
- 3 min read
What Is Supply Chain Management (SCM)?
Supply chain management is the management of the flow of goods and services and contains all functions that modify raw materials into final products.
It includes the active streamlining of an enterprise's supply-side actions to maximize consumer value and earn a competitive benefit in the marketplace.
SCM indicates an achievement by suppliers to generate and implement supply chains that are as efficient and economical as possible.
Supply chains cover everything from production to outcome development to the information systems wanted to direct these accomplishments.
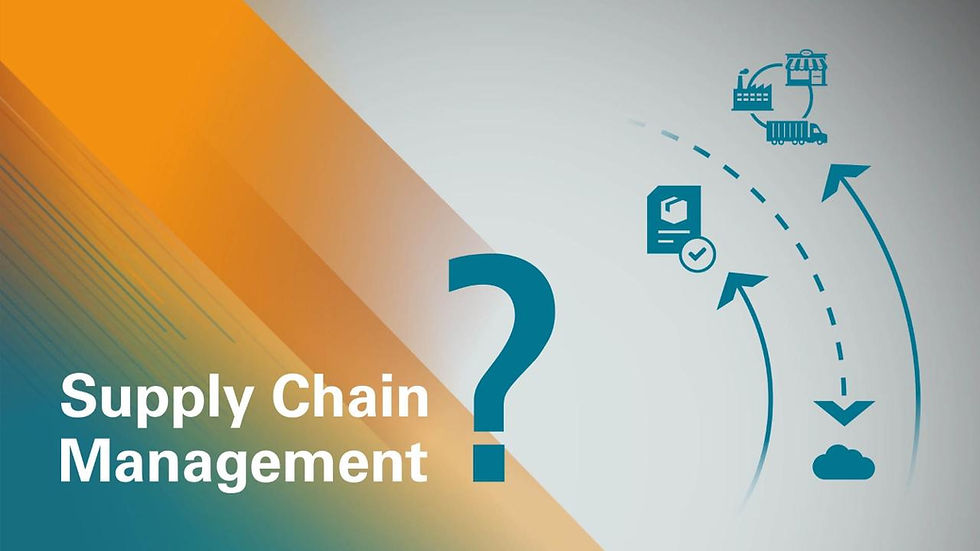
How Supply Chain Management Works.
Generally, SCM attempts to centrally control or link the production, shipment, and distribution of a product. By organizing the supply chain, firms can cut extra costs and submit products to the buyer faster. This is done by maintaining comfortable control of internal inventories, internal production, distribution, sales, and the inventories of firm vendors.
SCM is based on the idea that nearly every product that comes to market results from the efforts of various organizations that make up a supply chain. Although supply chains have existed for ages, most businessese only newly paid awareness to them as a value-add to their projects.
In SCM, the supply chain manager coordinates the logistics of all elements of the supply chain which contains five parts:
• The plan or strategy.
• The source (of raw materials or services).
• Manufacturing (focused on productivity and efficiency).
• Delivery and logistics.
• The return system (for inadequate or undesirable products).
The supply chain manager aims to minimize shortages and keep costs down. The job is not only about logistics and purchasing inventory.
The supply chain managers, “make suggestions to boost productivity, quality, and efficiency of operations.”
Improvements in productivity and efficiency go straight to the bottom line of a company and have a real and lasting impact. Good supply chain management holds businesses out of the headlines and away from costly recalls and lawsuits.
Supply chain.
A supply chain is the connected network of individuals, organizations, resources, actions, and technologies encompassed in the manufacture and sale of a product or service. A supply chain beginnings with the delivery of raw materials from a supplier to a manufacturer and ends with the delivery of the finished product or service to the end client.
SCM oversees each touchpoint of a firm's product or service, from preliminary innovation to the last sale. With so many places along the supply chain that can add value through efficiencies or lose value through expanded costs, adequate SCM can increase earnings, drop expenses.
MAJOR POINTS.
• Supply chain management (SCM) is the centralized management of the flow of goods and services and includes all processes that transform raw materials into final products.
• By managing the supply chain, companies can cut excess costs and deliver products to the consumer faster.
• Good supply chain management keeps companies out of the headlines and away from expensive recalls and lawsuits.
Why is supply chain management important?
Supply chain management is important because it can help achieve several business objectives. For instance, controlling manufacturing processes can improve product quality, reducing the risk of recalls and lawsuits while helping to build a strong consumer brand.
At the same time, controls over shipping procedures can improve customer service by avoiding costly shortages or periods of inventory oversupply.
Overall, supply chain management provides several opportunities for companies to improve their profit margins and is especially important for companies with large and international operations.
What are the five elements of supply chain management?

Supply chain management is often described as having five key elements: planning, sourcing of raw materials, manufacturing, delivery, and returns.
The planning phase refers to developing an overall strategy for the supply chain, while the other four elements specialize in the key requirements for executing that plan.
Firms must develop expertise in all five elements to have an efficient supply chain and avoid expensive bottlenecks.
Comments